HOW MOTORSKINS BRINGS TEXTILES TO LIFE
“TEXTILES THAT COME TO LIFE”
The way our members of Motorskins support the human body with the help of smart materials and textiles.
I remember reading their motto and thinking, “Whaaat? What does this mean?”. Intrigued as I was, I visited their website and saw a description that said “Berlin technology company specialised in textiles with embedded fluidics for human-machine interaction”, and that’s when I knew that they had lost me!
My name is Matthew, I am the Growth Project Manager at MotionLab.Berlin, and I thought, why not tell you more about Motorskins as part of the ‘How I did it’ blog series.
One of the most compelling things about being part of the MotionLab.Berlin community, with a ZERO technical background, is trying to make sense of the members’ projects. You literally feel like a 6 year old learning pure maths, which can be very frustrating. But trust me when I say that the rewarding silver lining is the, “Ah-haaah!” moment you have when you finally understand what the project is about!
I personally had such a moment with Motorskins, which is why I’m more than happy to write this article on them. Their cofounder, Facundo will confirm this as I must’ve said “ah-haaah!” at least five times when I asked him to tell me more about how they make their smart material product!
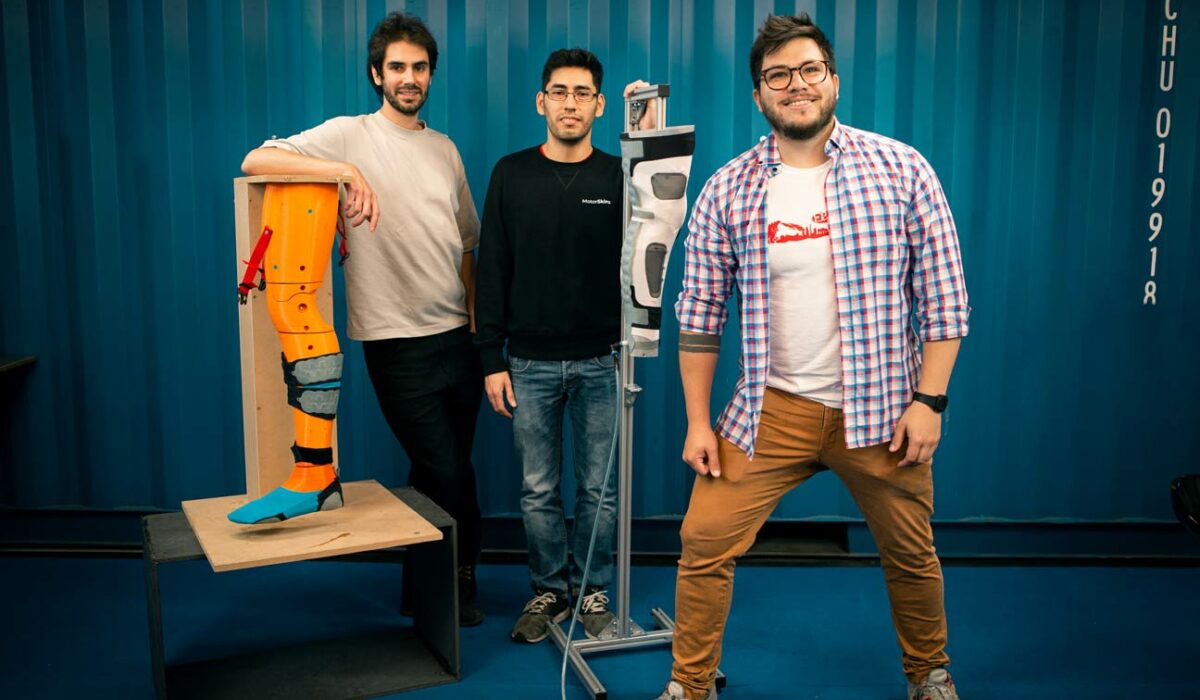
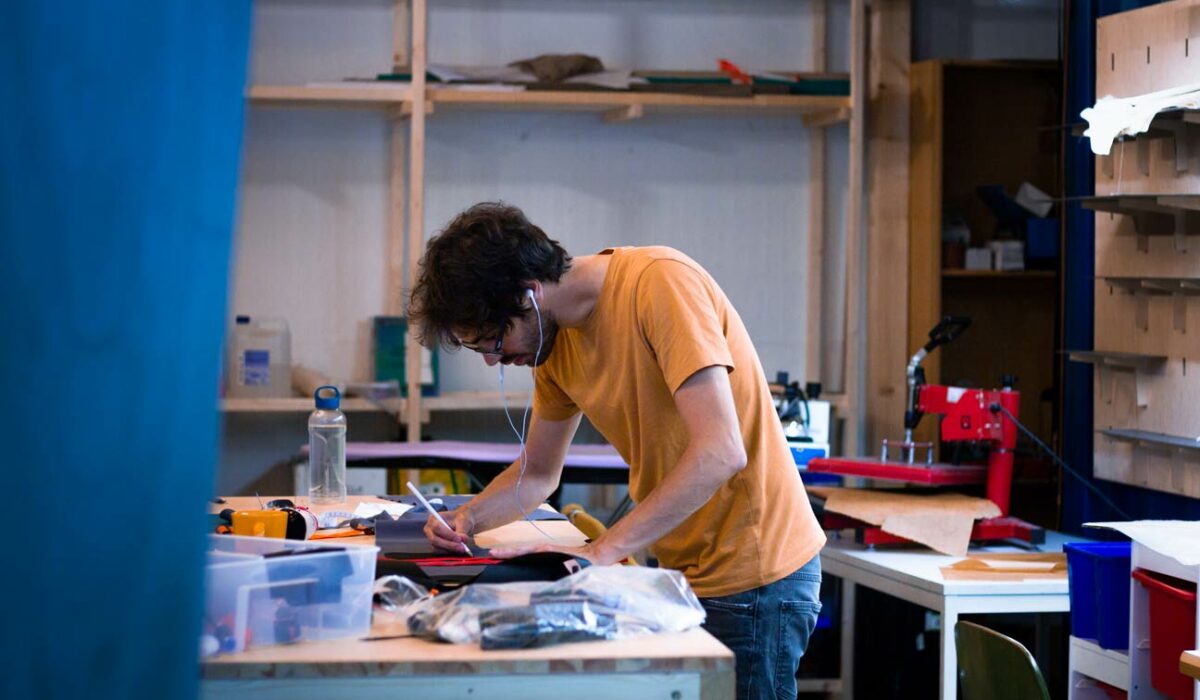
THE IMPORTANCE OF EXOSKELETONS
To understand what Motorskins does, is to understand exoskeletons and the benefits they hold.
Exoskeletons are external frames that support and protect an animal’s body. Additionally, they can provide an attachment framework for muscles, whereby they assist muscles in movement. In case you’re wondering if you’ve seen one, insects and turtles have them, whereas we, as human beings, only have an internal skeleton.
Our bodies are, to a certain extent, self-healing but every now and then we need additional support to give our bodies that extra push. This is where it gets interesting! Motorskins started doing research on plant and biological structures and their movements and asked themselves, “What would happen if we translated the principles of those biological structures and movements into textile-based designs and smart materials?”
They concluded that the design elements inspired by biological forms, could be applied to the body in different ways in order to support the body in performing various functions.
ROBOTIC FABRICS WITH EMBEDDED FLUIDICS
In a nutshell, Motorskins makes active and smart textiles that function as external muscles.
Exoskeletons for humans are not a new concept as you can find many different types of robotic and mechanical frames that help people overcome an injury or enhance their biological capacity. However, a lot of them are powered by electric motors that are complex, bulky and too expensive for the everyday person to afford.
Motorskins aims to democratise exoskeletons by creating soft robotics that enhance human movement in everyday situations. Given the bulky and mechanical form of existing exoskeletons, Motorskins looked to nature for simple, elegant and energy efficient solutions.
They create these solutions by combining two existing technologies which are hydraulics and textiles, since their product is fabric-based and they embed fluidics into the textiles using hydraulic technology.
HOW MOTORSKINS MAKE THEIR PRODUCTS
Normally, Motorskins would need an ultrasonic or laser welding machine to combine the two textiles, and a design tooling to create the form they inject the fluids in. This would be the easiest and most efficient way to create their smart material products, however the ultrasonic welding machine they need for the scale of their production ranges from €80k to €300k, whereas the design tooling would cost about €20k. Essentially, they would need a huge capital investment in the beginning, which we know isn’t easy to get as a hardtech startup.
Not only that, but the design toolings are specific to a certain mould, which means if they wanted to manufacture a different use-case, they would need another design tooling which is another €20k. Motorskins didn’t have an initial investment of more than €100k, therefore they had to look for another way to produce their smart textiles.
One of the things I find intriguing about our community is that a lot of the innovative projects you find in the space come about, when members don’t have the time or money to go for the most logical solution, so they go for one that works given the limited time and resources they have. And such is the case with Motorskins.
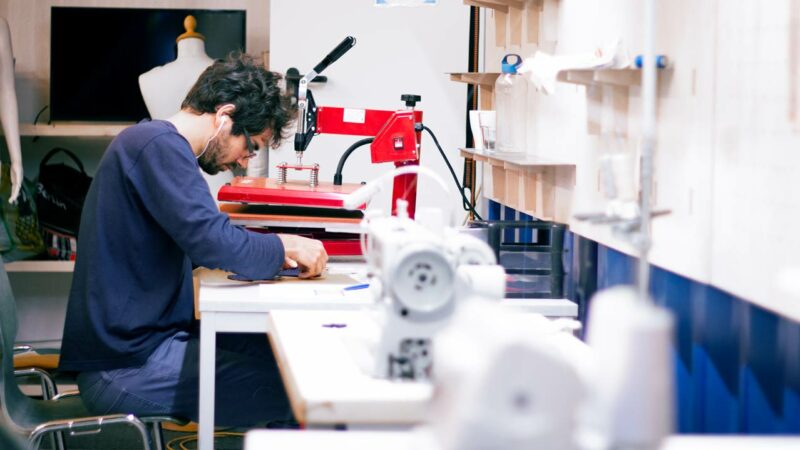
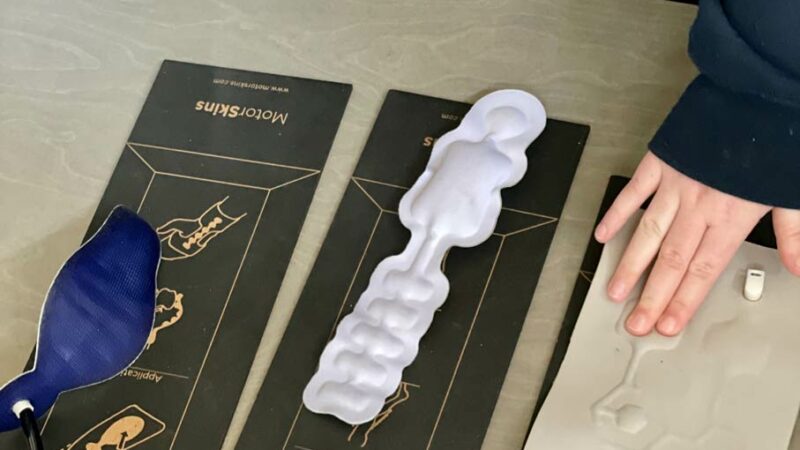
They use “Laser Catthi” of our partners GS Laser Systems to cut their smart textile parts, then they use their large format heat press to bond the two textiles together. However, since they embed the fabrics with fluidics, when they bond the two textiles together, they leave an air pocket or cavity between the textiles, in which they will pump the fluidics. The great thing about this process is that they slightly have more flexibility than if they used the ultrasonic welding machine and design tooling because they can shape the cavity between the two textiles whichever way they want.
After this, all they have to do is pump the fluidics into the smart material and voilà, the textiles will come to life! And as long as their production capacity is below a certain level, this will continue to be the cheapest option to create their exoskeletons until they scale up even further.
USE-CASES OF SMART MATERIAL EXOSKELETONS
On the one hand, they create smart material exoskeletons for medical purposes. Through compression technology, their exoskeletons can induce blood circulation in arms and legs, thus minimising the risk of diseases or conditions such as peripheral artery disease.
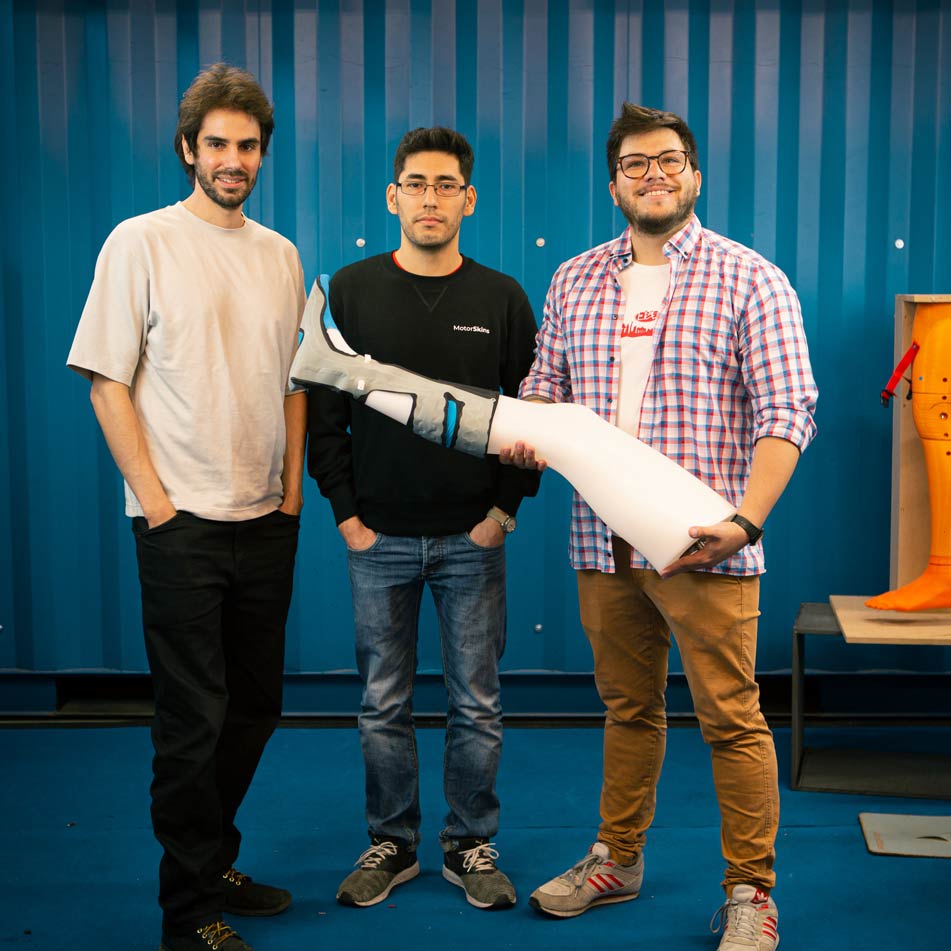
On the other hand, their exoskeletons can also be used for sports where athletes benefit from faster recovery. Additionally, we know that after a certain age, movement for the elderly becomes difficult due to varicose veins, therefore Motorskins’ exoskeletons is one solution to this challenge.
These are some of the use-cases they have explored so far, but there is definitely potential for more as this is just the beginning. A little bird tells me that in the near future you will find smart textiles embedded with fluidics in car interiors, furniture and fabrics for haptic feedback!
So far we’ve explored how one can use the laser cutters for wood, metal, smart materials and fabrics. With more examples loading, what kind of material or project would you want to try out in our laser cutting lab?